In today's fast-paced manufacturing landscape, the demand for speed and efficiency in product development has never been higher. Companies are constantly searching for methods to streamline their prototyping processes, and rapid injection molding has emerged as a game-changing solution. This innovative technique allows designers and engineers to create high-quality prototypes in a fraction of the time traditionally required, enabling them to accelerate their projects from concept to production.
Rapid injection molding not only reduces lead times but also enhances flexibility throughout the design process. By utilizing advanced technologies and materials, manufacturers can produce intricate parts that maintain dimensional accuracy and structural integrity. As businesses strive to stay ahead in a competitive market, understanding the intricacies of rapid injection molding becomes essential for anyone looking to optimize their prototyping efforts and bring their ideas to life faster than ever before.
Understanding Rapid Injection Molding
Rapid injection molding is an advanced manufacturing process designed to significantly reduce the time required to create injection molds. This technique is especially beneficial in prototyping, allowing designers and engineers to rapidly produce components for testing and evaluation. The process begins with creating a mold, which can be done using a variety of materials, such as aluminum or low-temperature thermoplastics. This choice of materials not only accelerates the molding process but also lowers costs compared to traditional steel molds.
One of the key advantages of rapid injection molding is the ability to iterate quickly. Designers can produce and test multiple iterations of a product within weeks instead of months. This speed is crucial in today's fast-paced market, where the ability to respond to feedback or changes in design can make a significant difference in a product’s success. With rapid injection molding , companies can refine their designs based on real-world performance, ultimately leading to better final products.
In addition to speed, rapid injection molding offers flexibility in production volumes. While traditional injection molding is optimized for large batch production, rapid injection molding accommodates small to medium production runs effectively. This adaptability makes it an ideal solution for startups and companies looking to test new concepts or enter niche markets without the financial burden of large-scale manufacturing. As a result, rapid injection molding is becoming an essential tool in the modern prototyping landscape.
Benefits of Rapid Injection Molding for Prototyping
Rapid injection molding offers a significant reduction in lead time, allowing designers and engineers to produce parts quickly and efficiently. Traditional injection molding can take weeks or even months to prepare tooling and start production, while rapid injection molding can often produce prototypes in just days. This speed allows teams to iterate on designs more frequently, making it easier to identify issues and integrate feedback, ultimately leading to a faster and more effective prototyping process.
Another advantage is the cost-effectiveness of producing low-volume prototypes. While traditional methods may require expensive, customized tooling for each project, rapid injection molding utilizes advanced techniques and materials that lower upfront costs for short runs. This means that teams can test multiple iterations of a product without the burden of excessive expenses, thus facilitating innovation and experimentation.
Moreover, rapid injection molding supports a wide range of materials and finishes, enabling the production of high-quality prototypes that closely resemble final products. This flexibility helps in accurately assessing aesthetic and functional aspects of the design. By using materials that mimic production-grade options, stakeholders can make informed decisions before committing to large-scale manufacturing. This quality assurance ultimately enhances the development process and leads to better final products.
Key Techniques to Optimize the Process
To truly master rapid injection molding, it is essential to focus on design optimization. Employing advanced software tools can help refine part geometries, allowing for reduced cycle times and better material flow. Designs should minimize complexity while ensuring the integrity of the final product is maintained. By implementing features like ribs and bosses judiciously, manufacturers can enhance strength while keeping the mold design straightforward.
Material selection plays a significant role in speeding up the prototyping process. Using high-flow materials can help reduce the cooling times and improve cycle efficiency. Additionally, selecting materials that are compatible with high-speed injection techniques will further enhance productivity. It's important to consult with material suppliers to identify the best options for your specific application, ensuring that the prototypes meet necessary performance criteria.
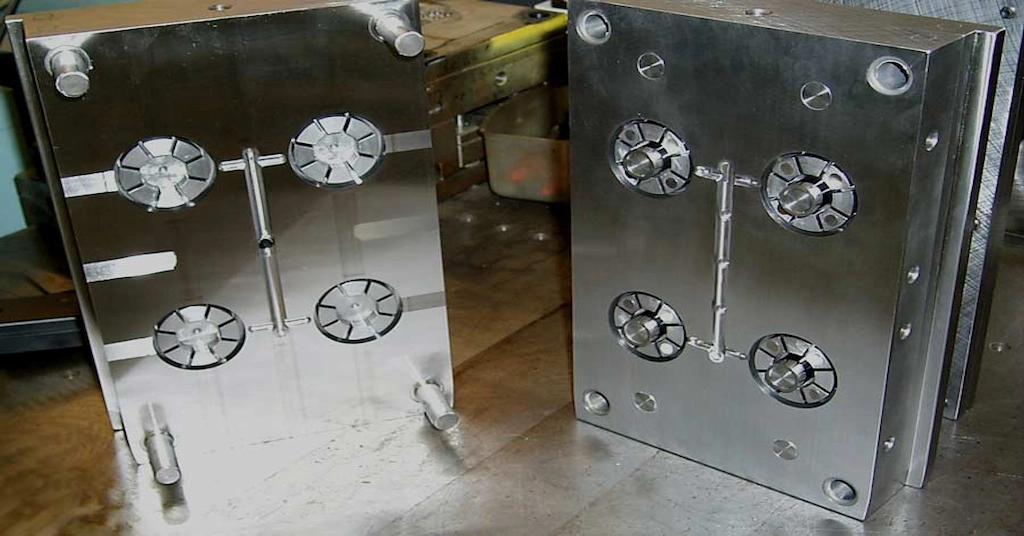
Lastly, investing in advanced machinery and automation can significantly improve efficiency in rapid injection molding. State-of-the-art injection molding machines with real-time monitoring capabilities can optimize operational parameters, leading to more consistent quality and reduced downtime. Automation of processes like mold changes and part removal allows for seamless operation and quicker turnaround times, making it easier to keep up with the demands of rapid prototyping.